Application of laser welding in hairpin motor
New energy motors are one of the key components of the three-electric system of electric vehicles. Together with the battery and electronic control system, they constitute the power source of electric vehicles.
Hairpin motor is also called flat wire motor,which is a motor that uses flat copper wire as the stator winding. Hairpin motors generally have higher efficiency and power density, which makes them particularly suitable for low-speed, high-torque conditions in new energy vehicles. In addition, flat wire motors also perform better in high temperature performance due to improved heat dissipation capabilities.It has been widely used in new energy vehicles.
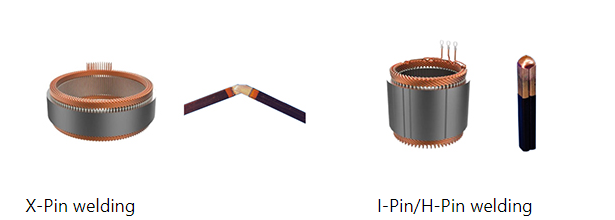
Industry difficulties
Due to manufacturing precision and cumulative errors, the position and shape of Hairpin will vary.If pre-welding measurements are not performed and a unified production process is adopted, defects such as missed welding and wrong welding will easily occur, which will lead to the scrapping of the entire product.Conductivity is an important indicator of weld quality, and solder joint penetration and Internal defects have a greater impact on the conductivity of the end ring. Conventional detection methods are slow to detect and cannot intervene in the welding process.
Newlaz Solutions
Newlaz independently developed the pin wire welding system of hair-pin motor through the integration of laser,2D/3D vision inspection, OCT detection and other technologies, real-time monitoring of the pin wire terminals welding H-Pin, X-Pin status, intelligent regulation of the output parameters, in order to achieve closed-loop intelligent high-quality and efficiency welding production.
Integration of welding and testing, real-time detection, adjustment, and quality control
- Pre-weld: focus height correction
- Pre-weld: Measure weld tracking
- During welding: real-time penetration measurement
- After welding: Post-weld morphology inspection
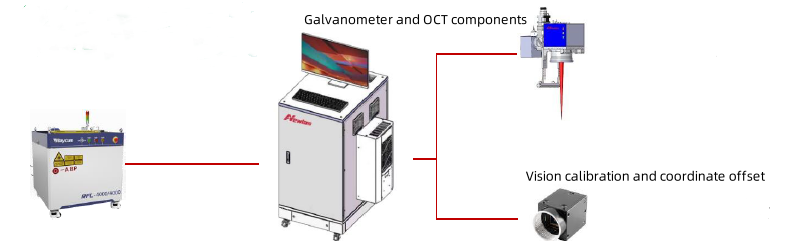
Technical advantages
By integrating scanning laser, visual measurement, coherent light detection and other technologies, the status of the end ring welding hair pin is monitored in real time and the output parameters are intelligently controlled to achieve closed-loop intelligent welding production. At the same time, a scanning welding process optimization method with energy input homogenization is adopted.
- Rapid detection and positioning
- Accurate control of galvanometer
- Real-time adjustment of power
- Real-time control of annular light spot (double beam)