At a time when new energy vehicles are booming, cylindrical batteries are becoming increasingly important in the power battery market due to their advantages such as high energy density, good heat dissipation performance, and good consistency. However, market demand is growing rapidly, and traditional welding processes have shortcomings such as low efficiency and insufficient precision under high production capacity requirements, which have become a key constraint on capacity expansion and quality upgrades. The Newlas cylindrical battery turret flight solution was born to meet the needs, injecting strong momentum into the industry’s high-quality and efficient production.
The game between tradition and new demands
- Efficiency bottleneck: The production capacity of traditional processes such as resistance welding and multi-laser head series connection is only 20-40PPM, which cannot match the large-scale demand for cylindrical batteries in new energy vehicles.
- Precision defects: Resistance welding has a large heat-affected zone and a high rate of false welding. The multi-laser head series connection is limited by the mechanical positioning accuracy, and the yield is difficult to guarantee.
- High cost: Traditional production lines occupy a large area, equipment investment and maintenance costs are high, and insufficient single-station production capacity restricts cost reduction and efficiency improvement.
Solving the problem – NewTFW cylindrical battery turret flying welding system
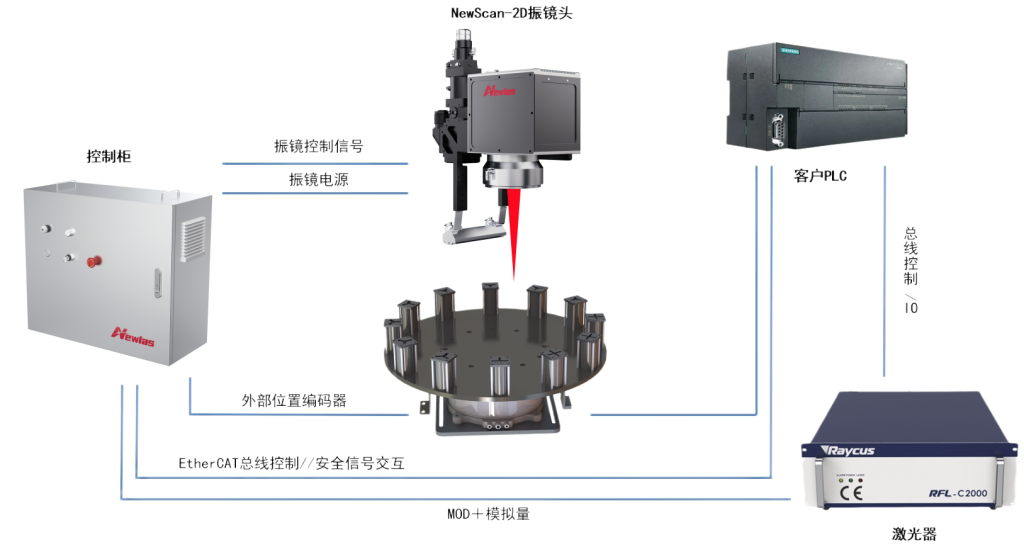
Product Introduction
- Key core technology: Newlas breaks through tradition and combines scanning galvanometer flight welding and turret transmission technology for the first time to accurately improve the welding efficiency of cylindrical batteries.
- Core functional components: Newlas’s 2D galvanometer welding head system NewScan and turret flight welding control system, including more than 1 million pulse encoders to transmit positions in real time, can accurately locate and achieve welding at the target position.
- Intelligent detection system: Newlas’s independently developed lens contamination detection system (collimator, field lens protection lens) and power monitoring system can be selected according to needs.
The turret flight welding system can adapt to the rotation of the turntable and implement dynamic flight welding for circumferential positioning tooling. Even if the turntable changes speed or runs at high speed, it can adapt to processing, which not only improves efficiency, but also ensures high precision and stable quality.
Features
1 Flexible module selection
Supports module selection (such as power monitoring module, protective lens pollution detection module, etc.), which can monitor power changes and lens status in real time during welding, strictly control welding quality, and effectively prevent power loss and poor welding.
2 High welding stability
Adopting high-standard optical materials and coating processes, with small thermal effects, it can meet the needs of long-term continuous welding operations at full power of 6kW level.
3 Strong versatility
Can adapt to a variety of lasers such as single-mode and multi-mode, and is compatible with domestic and imported mainstream brands; supports EtherCAT, Profinet and other protocols, and can interact with MES systems to make the production line intelligent and seamless.
Core Advantages
1 Variable speed flying welding: During the high-speed start-stop stage, the system can still ensure high-precision and high-quality welding under the extreme working conditions of the maximum acceleration and deceleration of 2000°/s;
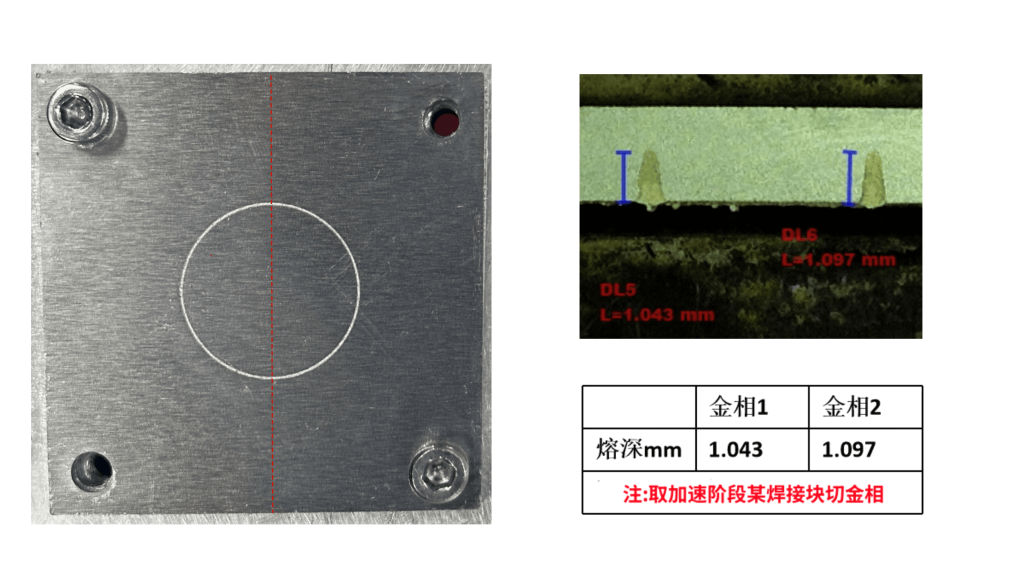
2 High-speed flying welding: the maximum supported turntable speed is 200°/s (line speed is about 1000mm/s);
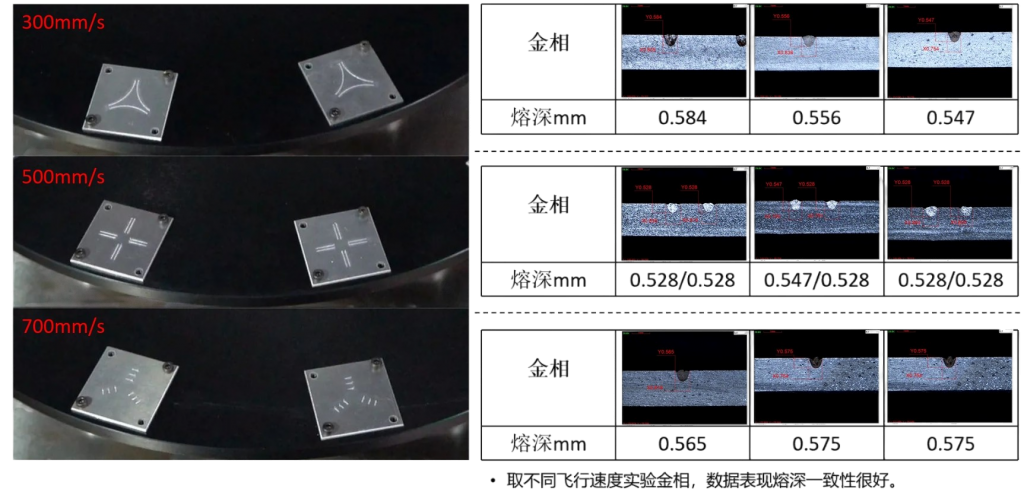
3 High-precision flight welding: the flight circle closing accuracy, flight repeated positioning accuracy and acceleration and deceleration flight positioning accuracy are all within ±0.1m;
4 Support a variety of complex graphics: support U-shaped lines, sine lines and other complex spline curves, compatible with CAD.dxf format drawing import, to meet customized needs.
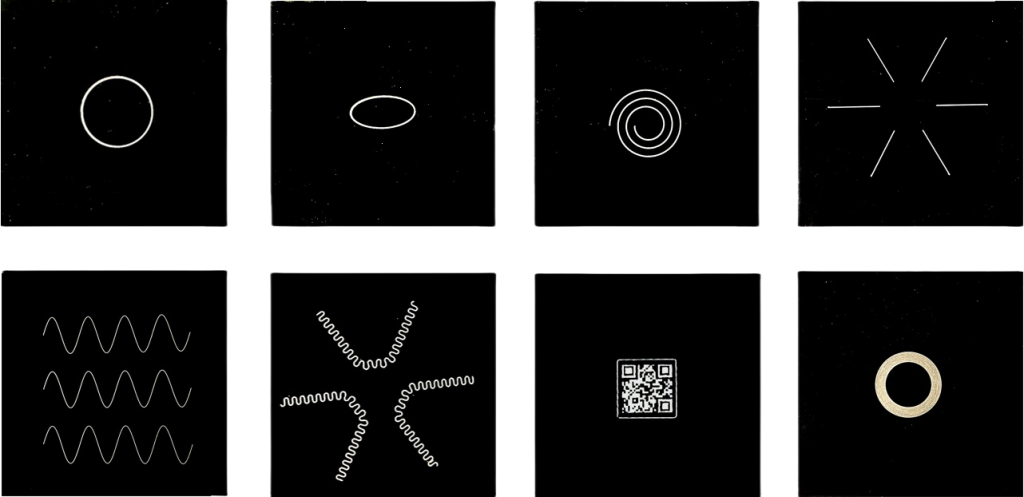
5 Workstation adaptability position compensation:
The product yield of the cylindrical battery production line is closely related to the accuracy of the product fixture. If there is a difference in the accuracy of the turret product fixture, the system will automatically compensate for the angle θ and R value according to the actual welding position of each workstation to ensure welding accuracy and product quality.
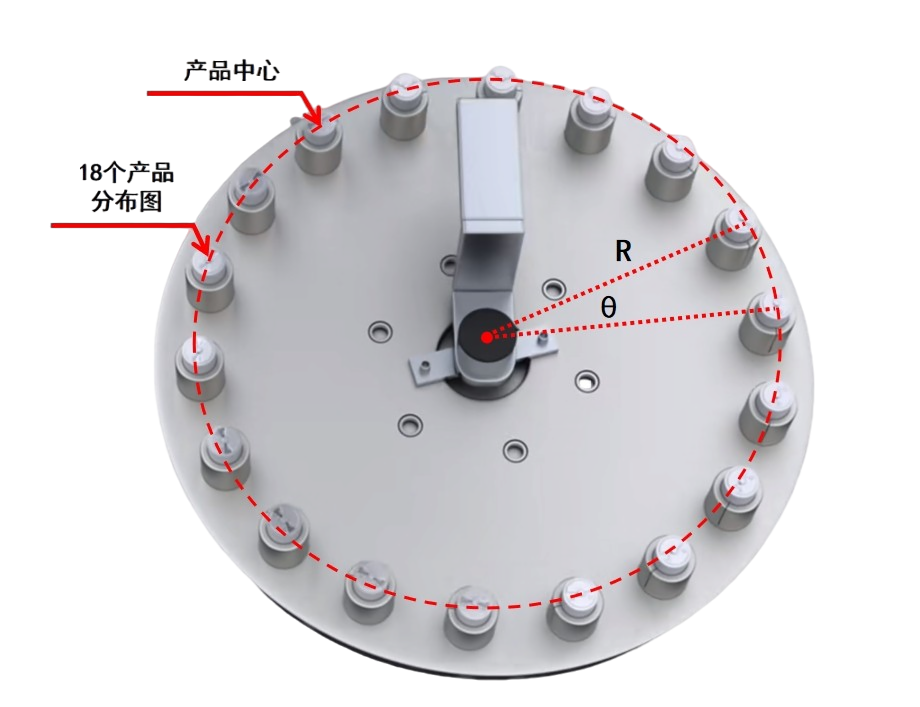
Applicable scenarios
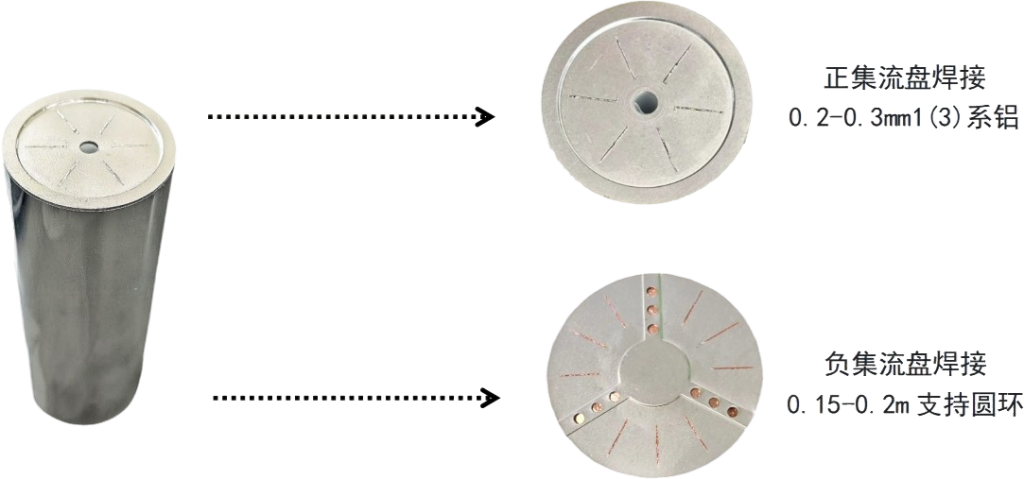
1 Welding
Suitable for welding of positive and negative collector plates, caps, cover plates and other parts of cylindrical batteries.
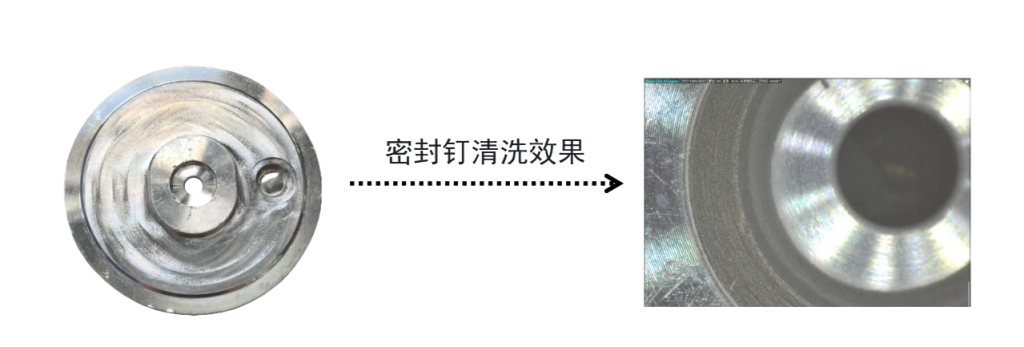
2 Cleaning
Supports circular and rectangular filling laser cleaning to meet the needs of different scenarios.
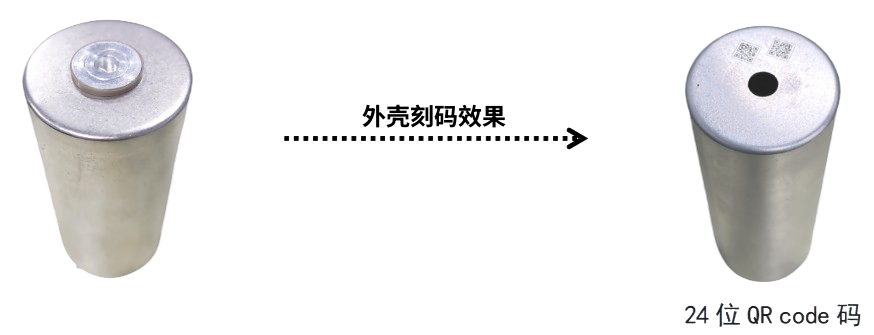
3 Engraving
Supports multiple sizes of coding such as 6x6mm to meet traceability and anti-counterfeiting needs.
The NewTFW cylindrical battery turret flight welding system, with its dual-core technology of “variable speed flight welding + intelligent station compensation”, directly faces the triple challenges of industry efficiency, precision and cost, and ensures welding consistency and yield rate from the source, providing a “high-precision, fully controllable, low-cost” one-stop solution for large-scale mass production of power batteries, helping automakers build core competitiveness with manufacturing efficiency in the new energy track.
【Product Pre-order】
Company website: www.newlas.com
Inquiry hotline: 189 7128 0299