Against the background of the “dual carbon” goal and global energy transformation, the new energy vehicle industry has ushered in explosive growth. As the core component of electric vehicles, the energy density, safety and manufacturing cost of power batteries directly determine the market competitiveness of the vehicle. As a key link in battery module packaging, pole connection and shell sealing, the welding process has increasingly stringent requirements for accuracy and reliability. With the advantages of high energy density, non-contact processing and automation, laser welding technology has become an inevitable choice for power battery manufacturing upgrades. However, industry pain points such as high reflectivity of aluminum alloys and frequent pore defects still pose severe challenges to the stability of welding processes. Achieving the “zero defect” manufacturing goal through material adaptation, process optimization and full-process quality control has become a core topic of collaborative innovation in the industrial chain.
1. Material property adaptation: Solving the dual challenges of aluminum alloy welding
Power battery shells and components generally use aluminum alloys (such as Al3003). Although its lightweight and high conductivity characteristics meet battery requirements, it also brings two major technical challenges:
- High reflectivity problem: Aluminum alloys have a laser reflectivity of up to 80%-92%, resulting in low energy utilization. By optimizing the laser waveform (peak wave, double peak wave) to improve the material absorption rate, and combining the galvanometer laser dynamic stirring technology to enhance the fluidity of the molten pool, the energy absorption efficiency can be effectively improved.
- Porosity crack control: Aluminum alloys have a high hydrogen content, and rapid cooling during welding is prone to hydrogen pores and thermal cracks, and the surface oxide film further affects the consistency of the weld. The use of pre-welding laser cleaning process, combined with welding speed optimization, can significantly reduce defects and improve sealing performance.
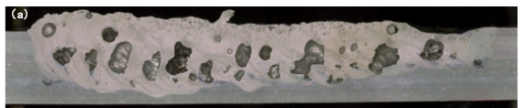
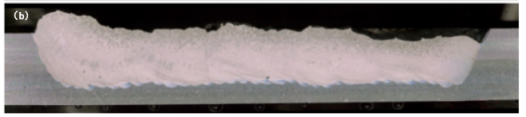
Image source: Shanghai Institute of Optics and Precision Mechanics
2. Precise matching of processes: customized welding solutions for component structure and performance
For the diversified structures (shell, pole, busbar) and performance requirements (sealing, strength, efficiency) of power battery components, differentiated laser welding processes are required:
- Heat conduction welding: suitable for thin plate welding scenarios such as battery shell and cover plate sealing, with wide welds and small heat-affected zones, but relatively shallow penetration.
- Deep penetration welding: specially designed for high-strength connections such as poles and explosion-proof valves, deep penetration is achieved through high power density, effectively controlling workpiece deformation.
- Pulse-continuous compounding: for highly reflective materials such as aluminum and copper, pulsed laser can reduce spatter, while continuous welding can improve welding efficiency, especially suitable for long weld processing scenarios.
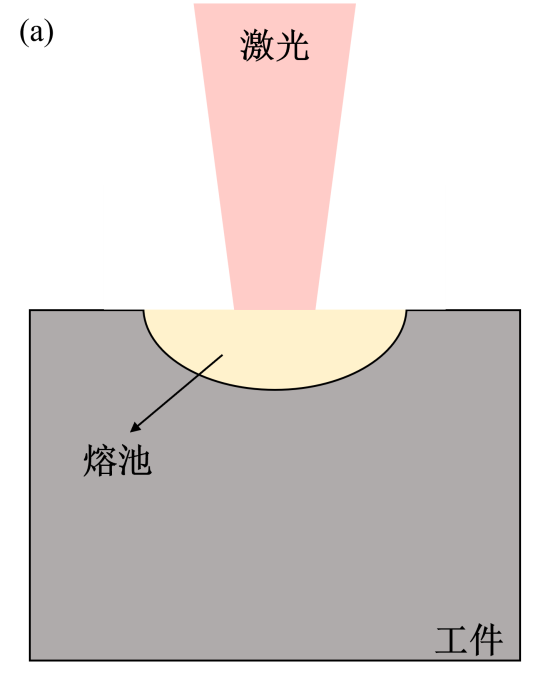
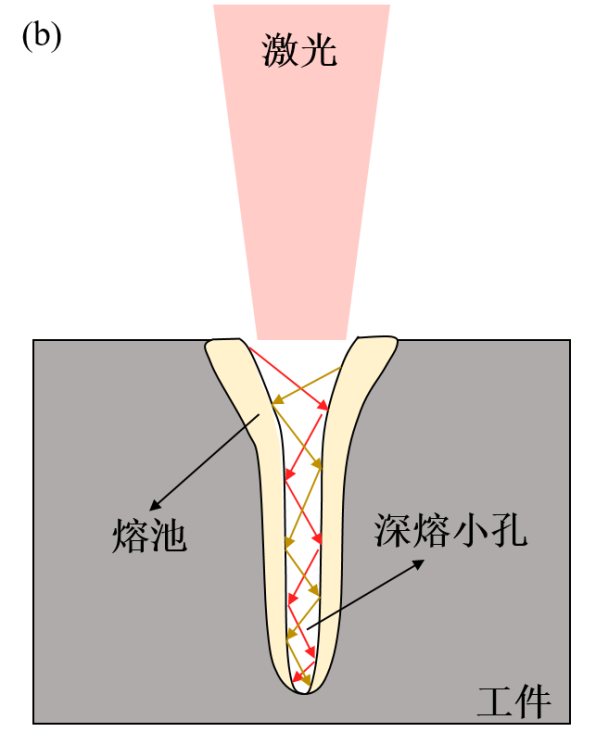
3. Dynamic parameter optimization: a precise balance between efficiency and reliability
The quality of power battery laser welding is highly dependent on the dynamic regulation of core parameters:
- Power density regulation: The penetration depth is directly related to the beam power density. The focus is usually positioned at about 1/4 of the penetration depth below the workpiece surface to ensure sufficient power density.
- Speed adaptive adjustment: The welding speed has a significant impact on the penetration depth. The optimal speed range needs to be determined under specific power and material thickness to achieve maximum penetration while avoiding false welding or welding penetration.
- Shielding gas selection: Helium is suitable for deep penetration welding scenarios and can effectively suppress plasma; argon provides balanced protection; and nitrogen meets the needs of cost-sensitive applications.
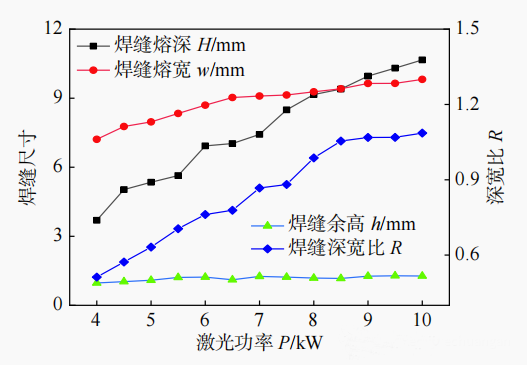
Image source: Zhihu
4. Full-process quality control system: the path to achieve zero-defect manufacturing, building a “prevention-monitoring-feedback” three-in-one quality assurance system:
- Equipment health management: regular maintenance to ensure that the equipment is in the best working condition and eliminate welding defects caused by equipment factors.
- Workpiece pretreatment standards: strictly control pollutants such as dust and oil, and use the “preheating + seam welding” process to treat key parts such as poles and explosion-proof valves.
- Online real-time monitoring: through real-time analysis of weld images, accurately identify defects such as pores, cracks, and incomplete penetration, and continuously improve product yield.

5. Innovative solution: NewOCT laser welding penetration real-time monitoring system
- Online penetration detection: integrated OCTMetrix module to achieve real-time monitoring of penetration during welding process;
- Plug and play design: modular architecture compatible with mainstream welding heads (galvanometer/swing head/fixed focus head);
- Pollution warning function: optional lens pollution detection module to prevent welding abnormalities caused by power loss;
- High stability guarantee: using high temperature resistant optical materials, supporting 8kW full power continuous operation;
- Multi-scenario adaptation: compatible with single mode/multi-mode/ring spot lasers, covering mainstream brands at home and abroad;
- Industrial interconnection capabilities: support Modbus TCP/PN/EIP and other communication protocols, seamlessly connected to MES system.
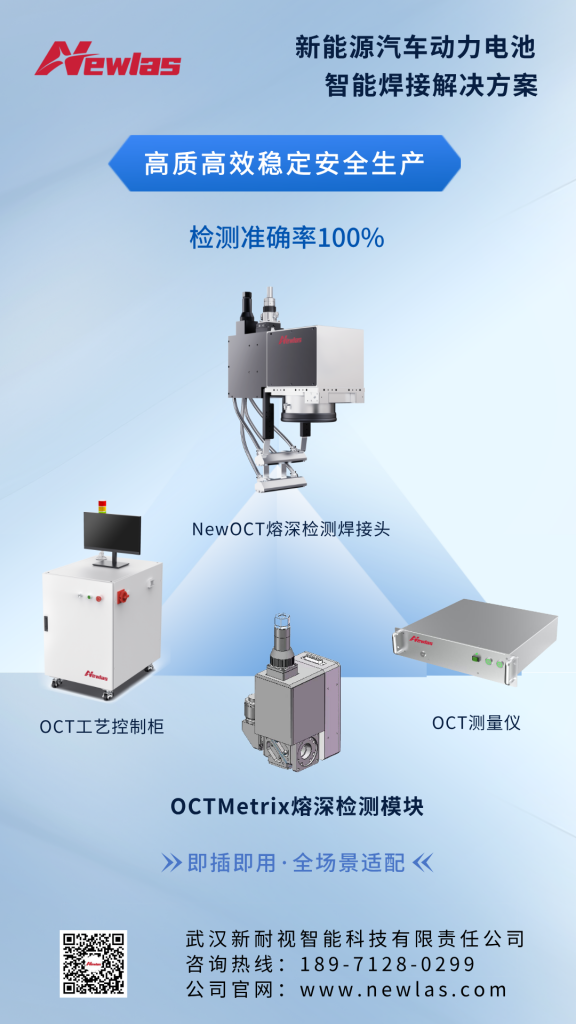
As an innovator in the field of laser welding, the NewOCT system realizes an integrated welding-detection solution through the deep integration of galvanometer control and optical coherence tomography (OCT) technology. At present, the system has been applied on a large scale in leading enterprises in the industry, providing “zero defects, zero rework” full-process quality assurance for power battery welding production lines. NewOCT continues to promote the upgrading of industry standards with technological innovation, and helps the new energy vehicle industry move towards a new era of “zero defect intelligent manufacturing” through a solution matrix of improving quality and efficiency, reducing costs and safety, and flexible expansion.In the future, the company will continue to deepen its roots in the field of laser welding quality inspection and provide global customers with smarter and more economical innovative solutions.
Product reservations
Company website: www.newlas.com
Inquiry hotline: 189-7128-0299