Laser brazing has the advantages of high efficiency, precision and no pollution. It can improve the strength and rigidity of the car body while reducing the weight of the car body. Among them, the roof laser brazing has the longest length, the highest quality requirements and the greatest control difficulty. The stability and reliability of its welding quality are crucial for ensuring the safety of the car body. The following will introduce the application of NewLBO 3D weld seam positioning and quality inspection system in automobile roof welding.
Ⅰ.Principle of laser triangulation
NewLBO 3D vision inspection uses the principle of laser triangulation to measure the height of the workpiece surface. Based on three-dimensional vision measurement with line-structured light, by adding a displacement in the motion direction, the height information of the workpiece surface is obtained, thereby realizing high-precision dimensional measurement and defect detection.
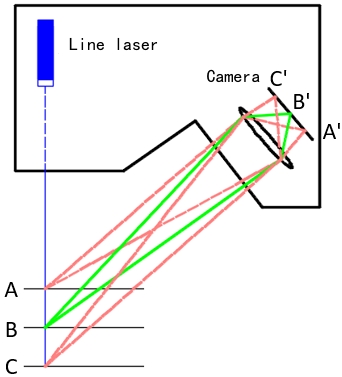
II. Introduction to NewLBO 3D Weld Seam Positioning and Quality Inspection System
The NewLBO 3D weld seam positioning and quality inspection system mainly consists of a 3D camera, a robot and a weld seam detection software processing system. The 3D camera is used to collect three-dimensional data of the surface morphology of the inspected weld seam. During the movement of the robot, the weld seam detection software quickly analyzes high-density point cloud data to detect weld seam quality, and realizes measurement of weld seam length, width, depth/height. It can detect defects such as pores, missed welds, collapses, weld beads, and spatter. At the same time, it completes the interaction and feedback with external signals, loading and saving of data parameters, etc. With a real-time interface, the scanned morphology and analysis results can be manually viewed.
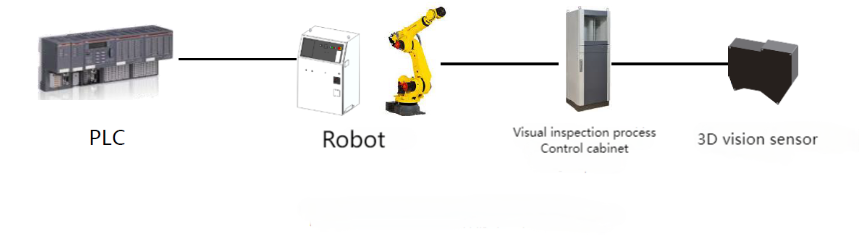
Advantages
- Efficient and reliable defect identification and detection.
- Customized weld geometry measurement.
- Weld position change detection.
- Online/offline analysis with result visualization.
- 2D/3D graphical reproduction of weld details.
III. Application of Product
2D Defect Identification
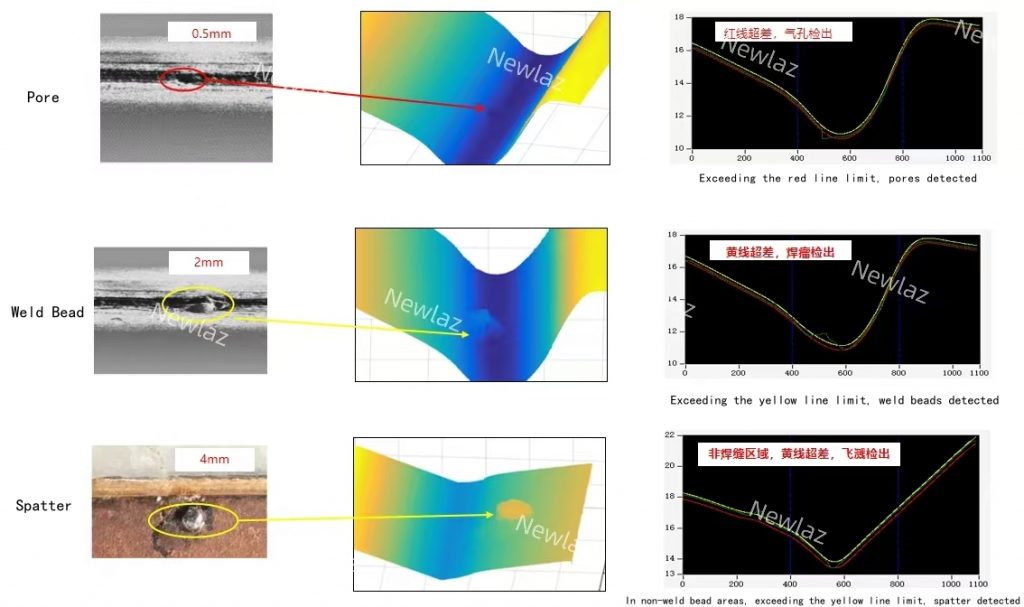
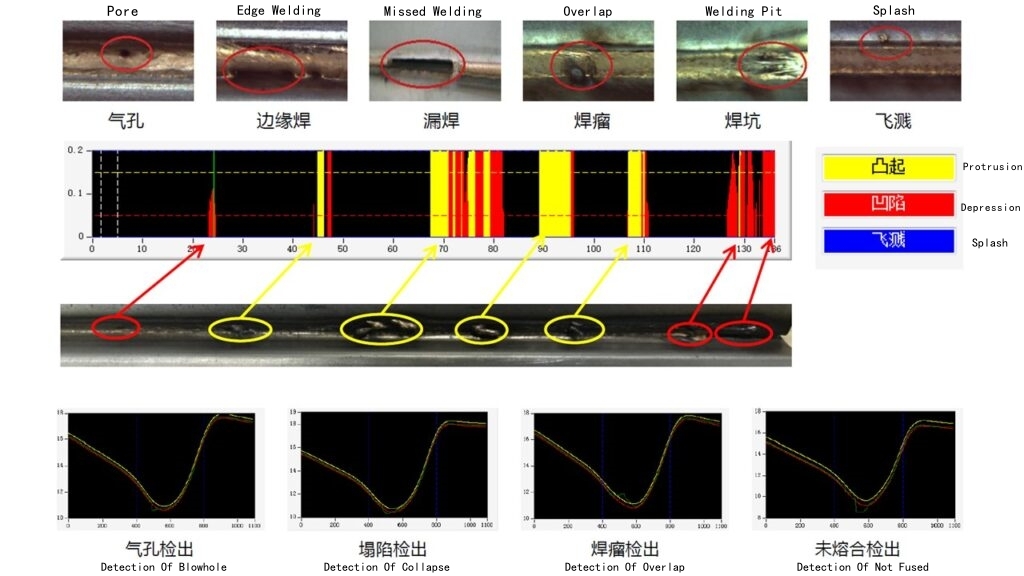
3D Defect Identification
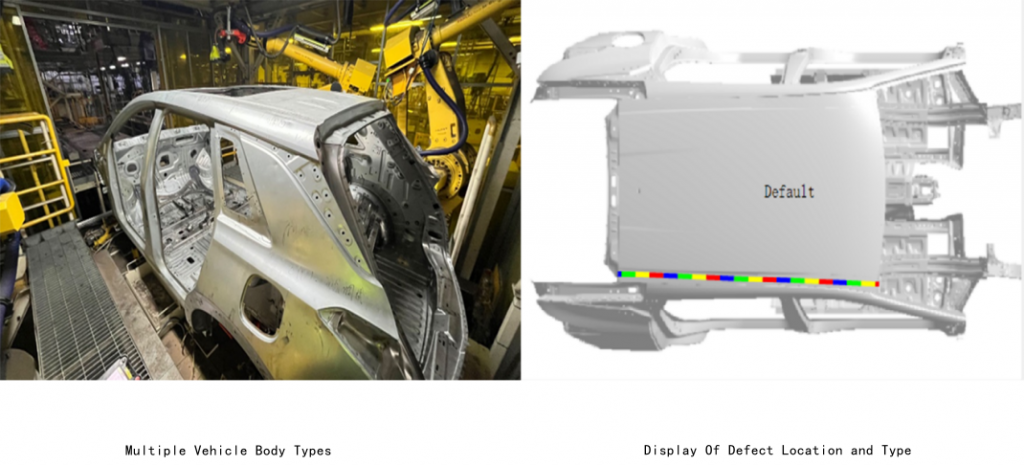
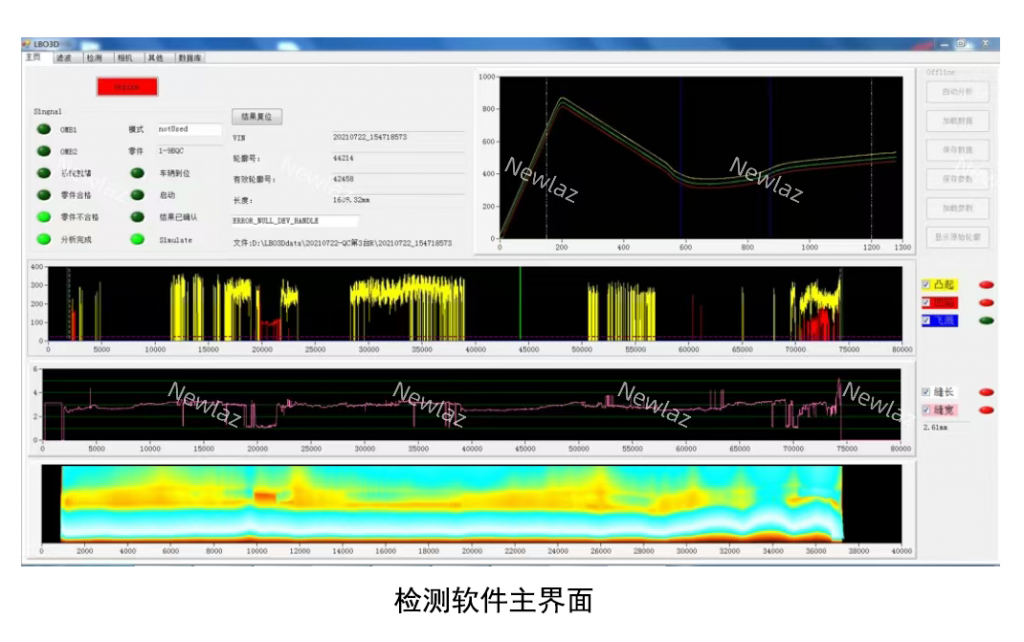
Live Situation of On-site Detection
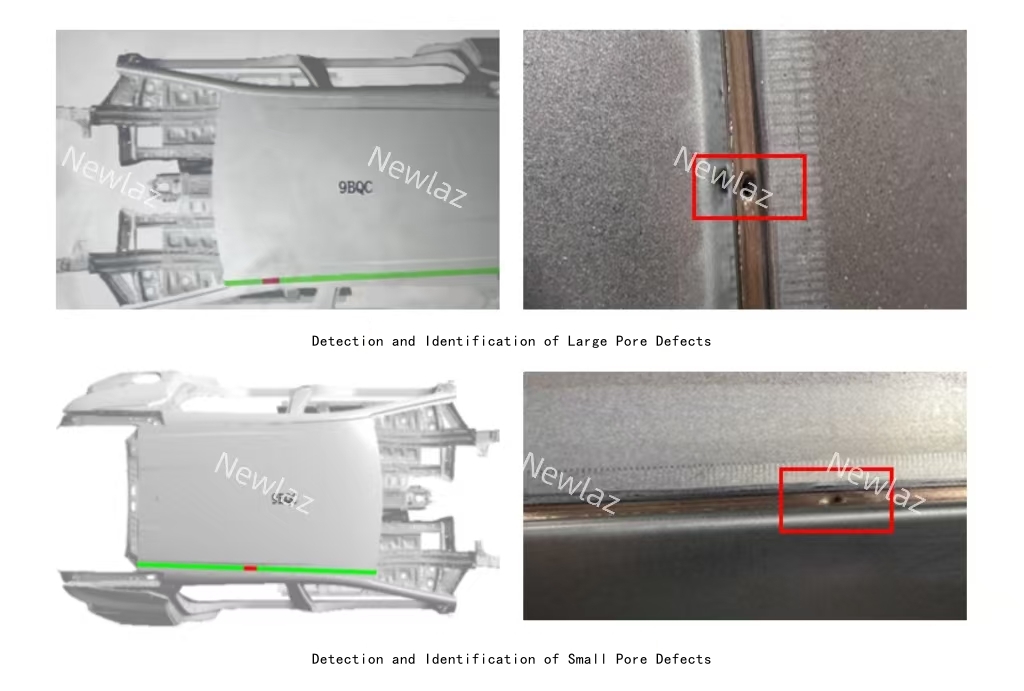
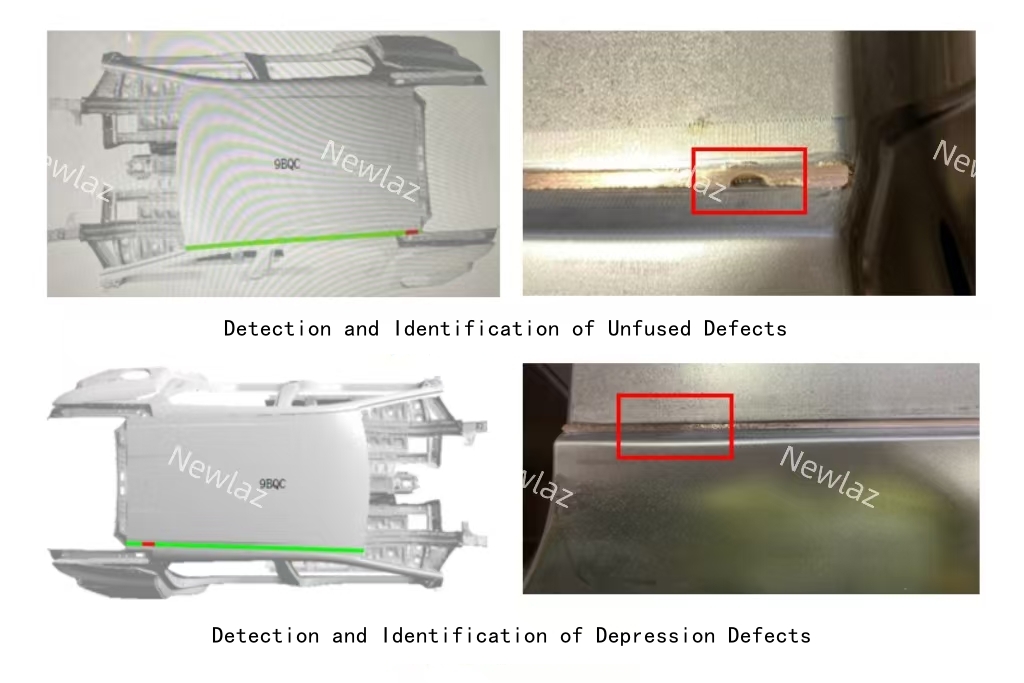
The application of laser brazing in the manufacturing of automotive roof and side panels not only offers weld strength and good weld appearance that are unparalleled by traditional spot welding and MIG/MAG welding, but also features high welding efficiency. It has become the standard process for automotive roof manufacturing. To facilitate production managers to keep abreast of the welding situation at any time and conduct quality control in real time, NewNextsight has developed the NewLBO 3D weld seam location and quality inspection system, which can detect the weld defects online during the welding process, significantly reducing the time cost, making the production more efficient and effortless, and achieving automated, flexible and intelligent automotive manufacturing.