On August 14, the second day of the 27th Beijing Essen Welding &Cutting Fair, the “2024 Technical Seminar on Intelligent Factories for Automobile Welding and Assembly” jointly organized by the Chinese Mechanical Engineering Society and the Jiangsu Mechanical Engineering Society was held in the N5-M50 conference room of the Shanghai New International Expo Center. This conference invited a large number of outstanding experts from vehicle manufacturing enterprises, robot manufacturing enterprises, universities, and scientific research institutes to gather together to jointly discuss new intelligent technologies and new processes in automobile welding.
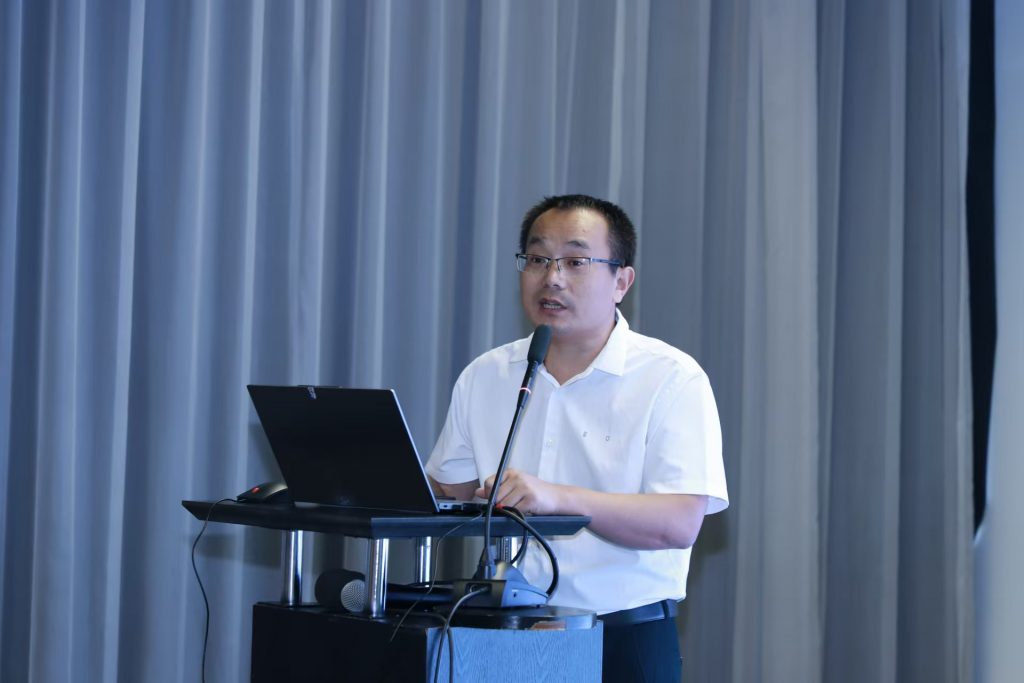
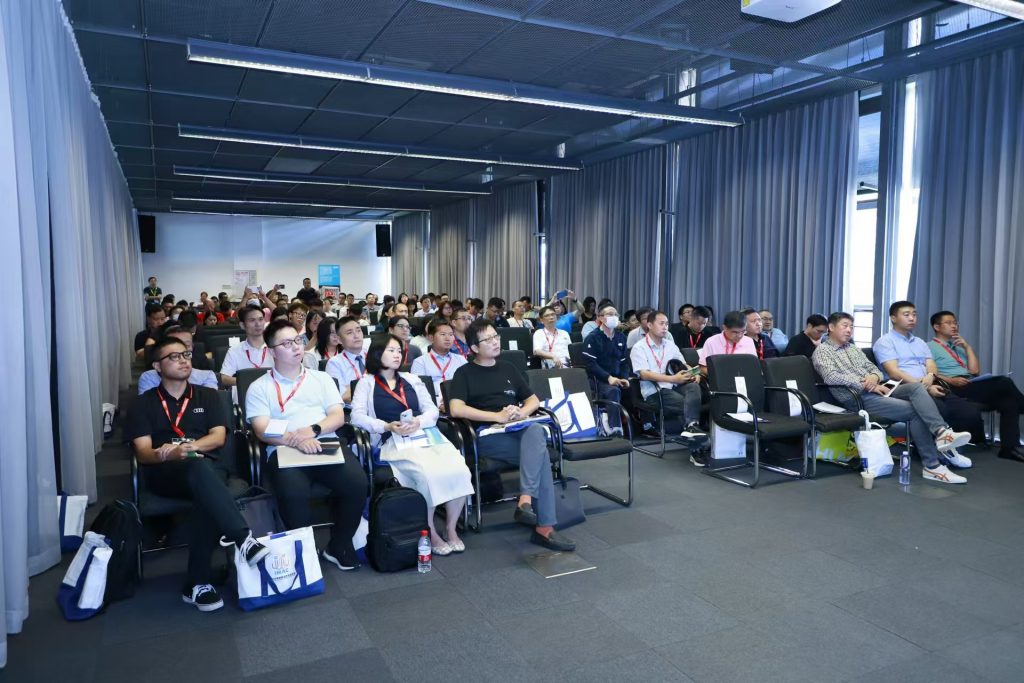
Liu Gang, process director of Newlaz, said that with the continuous development of new energy vehicles, the power battery structure is also continuing to evolve, from the early independent battery pack module gradually evolved into the battery body integration design, through the integration of the battery and the body, the battery body integration technology to achieve maximum space utilization and higher integration.
The application of Newlaz on-the-fly laser welding technology in the integrated manufacturing of new energy vehicle body and battery pack, combining efficient laser connection technology with innovative material forming process, can effectively improve the stiffness of the body and the flexibility of the body in white manufacturing, significantly reduce the investment in standard equipment and fixture investment, and reduce cost and efficiency for end users.
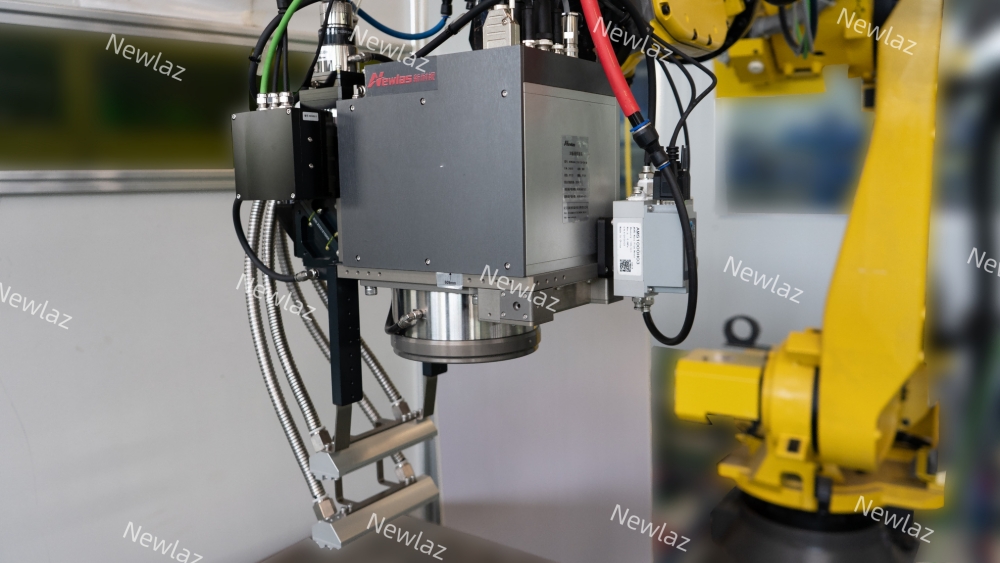
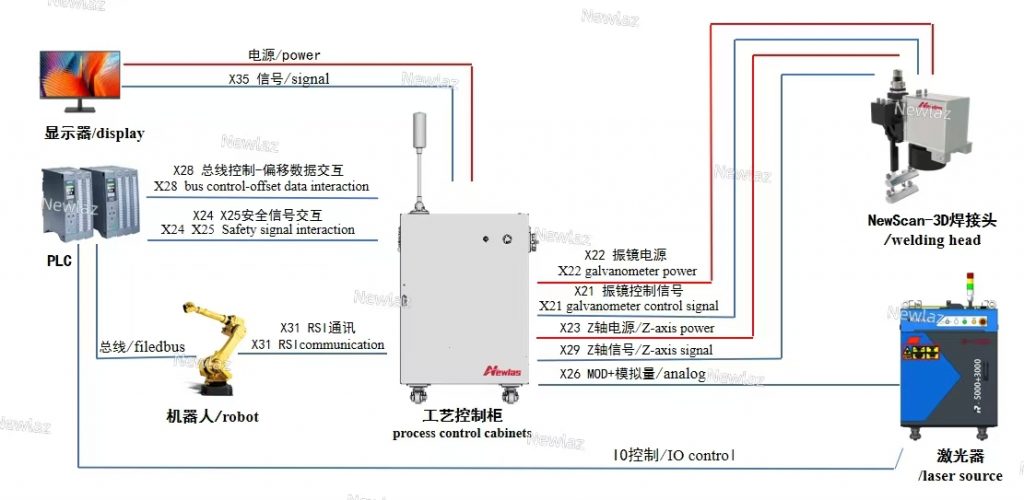
The Newlaz laser flight welding subsystem adopts the independently developed NewScan-3D galvanometer on-the-fly laser welding head (NewScan-3D), which has leading repeatability accuracy and zero drift interpolation algorithm, and has stable and reliable performance in welding applications such as linear welds,C-shaped weld seam, and flight spiral welding, meeting the needs of integrated manufacturing of battery pack and chassis. It is committed to creating convenient and lightweight electric vehicles.
-Highlights of products-
- On-the-fly spiral spot laser welding for higher connection strength
For the high-strength steel connection process such as the body in white side, the strength of laser spiral spot welding can easily exceed the resistance spot welding, achieve higher connection strength, and the area and number of stations of the welding area can be reduced by more than 50%.
- On-the-fly laser welding enables innovative applications of CTB battery packs
The laser welding is used to connect the front compartment, the left and right connecting beam and the rear bottom plate of the battery pack of the body-in-white chassis, which has high strength, flexible welding position and attitude, and can realize the connection of dissimilar metals.
- High speed and high efficiency, greatly improve production efficiency
The remote welding characteristics of the laser eliminate the adaptation of the body in white manufacturing process and the space limit of the welding gun avoidance, greatly reduce the number of fixture input and station space input, and reduce the manufacturing time.
The successful holding of this seminar has created a favorable exchange and interaction platform for the green and efficient development of automotive welding smart factories, and promoted the sharing and exchange of technology and experience in the industry. In the future, the company will continue to achieve technological innovation and intelligent application, and continue to make new breakthroughs in improving production efficiency, ensuring welding quality and reducing input costs, so as to provide high-quality products and services for the market and help China’s manufacturing transformation and upgrading.