Foreword
With the improvement of performance requirements for power batteries in new energy vehicles, laser welding, as an efficient and precise welding method, is widely used in the manufacturing process of new energy vehicles for the welding of body-in-white and power batteries to meet the needs of lightweight and improved safety performance in new energy vehicle manufacturing.Newlaz Flight Welding Height Real-time Tracking Vision System recognizes the center height of power batteries through 3D cameras, tracks the flight welding effect in real time, and improves the production cycle. The height measurement and flight welding are completed in the same workstation, streamlining the production process and making the flight welding process more automated and intelligent.
Ⅰ.The Disadvantages of Traditional Detection Methods
- Welding Delay Caused by Position-Finding Method
The traditional position-finding method requires that the 3D camera collects all the parts to be welded completely, and then analyzes to obtain the position and height information of the welding parts. The welding process is obviously lagging behind the data collection process of the 3D camera.
- Complicated Welding Process in Dual Workstations
The traditional welding process is divided into two workstations, and the positioning workstation and the welding workstation alternate. Not only does it occupy space, but also the robot needs to measure the height information of the power battery separately in the positioning workstation in advance, set the trajectory height, and then enter the welding workstation to start welding. The process is cumbersome.
II. System Introduction
- System Principle
A 3D camera is placed in front of the galvanometer welding head to collect the surface height of the power battery in real time. The deviation value of the height of the surface to be measured is analyzed and the height of the galvanometer is adjusted in time to achieve the effect of real-time height tracking and flying welding.
- System Components
The real-time height tracking vision system for flying welding mainly includes a 3D camera, an industrial personal computer (including vision software), and is also equipped with a flying welding system, a robot (or a three-axis platform), PLC, etc.
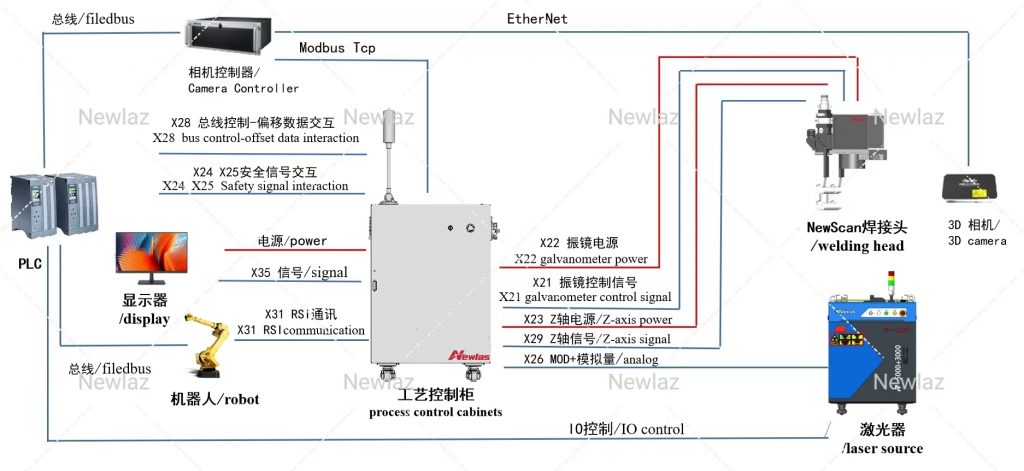
Ⅲ.Advantages Of System
- The time of height measurement coincides with the welding process, effectively improving the production cycle;
- The height measurement and flying welding are completed in the same workstation, which can effectively save production costs and improve the utilization rate of the site;
- The point cloud analysis and data sending process are stable, and the overall time consumption is less than 0.2s, ensuring the reliability of the tracking process;
- It can be flexibly applied to robot platforms and three-axis platforms, and the height measurement accuracy is < 0.1mm;
- It can be adapted to a maximum flying speed of 300mm/s;
- It has anti-stupid judgments such as the height of the busbar, the extreme difference in height, position, and spacing.
Ⅳ.System Application
It is mainly applicable to the real-time measurement and feedback of the height of the busbar during the laser flying welding process of the new energy power battery BusBar. The height of the flying focus of the galvanometer can be adjusted in time to ensure the welding quality.
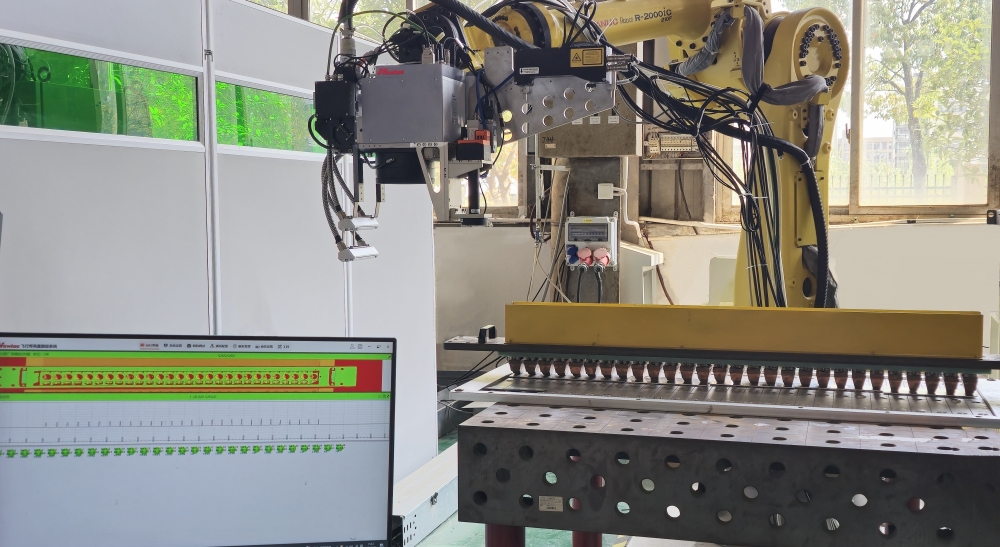
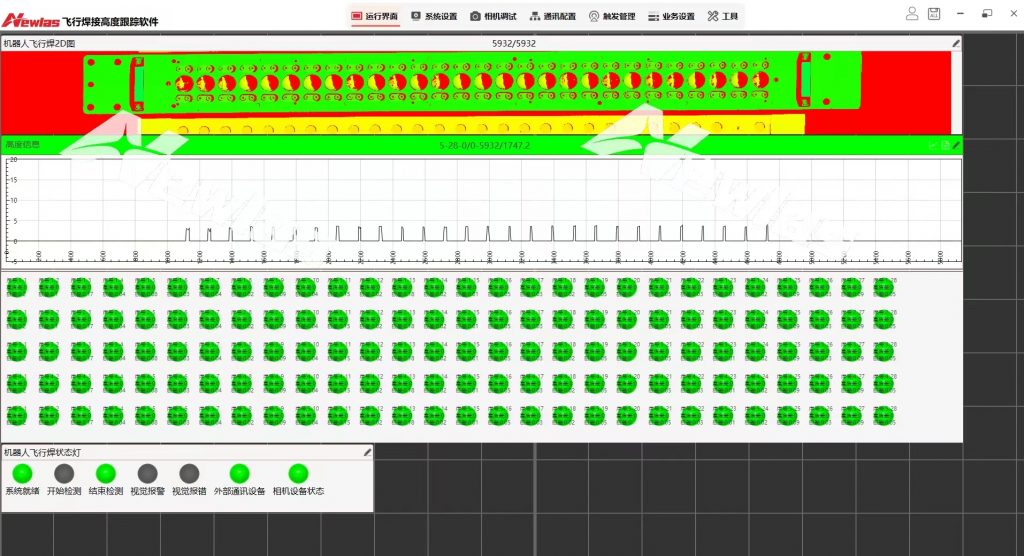
Conclusion
With the continuous progress of technology and the sustained development of the manufacturing industry, Newlaz will focus on the demands of high quality, high efficiency and cost reduction in laser welding, and continuously upgrade the performance of on-the-fly welding products, including related detection systems, to adapt to more complex and diverse production scenarios, further improve the welding quality and efficiency, achieve a higher degree of automation and intelligence, and provide strong support for the transformation and upgrading of the manufacturing industry.