With the development of times and advancements in technology, the industrial sector, which strives for high-efficiency, high-precision production, is constantly raising its requirements for welding quality, efficiency, and precision. Newlaz 3D vision weld seam guidance system employs cutting-edge 3D vision technology to adapt to complex environments through flexible multi-point guidance, and one-click high-precision hand-eye calibration to establish coordinate mapping and ensure reliability. This system will drive welding production towards intelligence and automation, enhance production efficiency, and create higher economic value.
Ⅰ.The defects of welding robots
In actual production, industrial robots often adopt the teaching and playback mode, which has high requirements for the processing accuracy of the pre-welding process, the accuracy of tooling and the control of welding thermal deformation. Any minor deviation may lead to a decrease in welding quality, an increase in the reject rate and rework costs.
Therefore, enterprises often face the following pain points:
1.High investment in the improvement of the pre-process
Upgrading and improving the processing equipment of the original process and designing high-precision tooling require a large amount of funds and huge investment.
2.High cost and inconsistent quality of manual repair welding
When welding robots starts working, due to problems such as poor consistency of base materials, tooling deviations and thermal deformation, manual repair welding is often required, which increases labor costs and makes it difficult to guarantee product quality.
3.Large expenditure and low profit in multi-variety and small-batch production
When there are many varieties and small batches of welded workpieces, enterprises need to spend the equivalent of large-scale production in terms of manpower and material resources in the early stage to ensure process stability, and the profit is meager.
To improve the processing efficiency of welding robots, reduce the cost of use, and reduce the time and difficulty of teaching, NewLaz has launched a 3D visual weld seam guidance system, aiming to comprehensively solve a series of problems such as weld seam tracking and positioning, and help welding robots operate efficiently in production.
II. System Principle
- Weld seam positioning: It refers to the process of locating the weld seam using one or more searches. The joint to be welded is accurately located by moving the welding robot or editing the machine program path before welding.
- Weld seam tracking: It refers to installing an optical sensor in front of the welding position for data acquisition, and then transmitting it to the welding robot. Various adaptive fuzzy control algorithms are used to correct the trajectory of the welding robot or special machine to achieve adaptive control and real-time weld seam tracking.
III. System Characteristics
1.One-click high-precision hand-eye calibration, quickly and accurately establish the mapping of the camera and the robot tool coordinate system, laying the foundation for high-precision welding;
2. Flexible multi-point guidance for welding, adapting to complex application scenarios
Standard position guidance Offset position guidance
P.S:Currently, it has the welding guidance ability for various typical groove types (fillet joint, butt joint, lap joint, etc.), and support customization for other special groove types
3.Product Unique Value:
Highly stable and high-precision hand-eye calibration algorithms provide a solid guarantee for the reliability of the guidance system;
High-precision cameras and guidance algorithms determine the accuracy and adaptability of visual guidance.
Ⅳ.Advantages Of System
1.Cost savings
To ensure welding quality, enterprises invest heavily in the improvement of base materials, tooling, and incoming welding workpieces, including equipment updates and the purchase of high-precision tooling. The new Nvision 3D vision weld seam guidance system can significantly reduce this expenditure.
2.Quality improvement
Problems such as workpiece clamping deviation and thermal deformation often occur during the operation of traditional welding robots. Manual repair welding after welding is frequent, resulting in increased costs and a rising repair rate. This system effectively solves these problems and significantly improves the welding quality.
3.Efficiency improvement
The precision of the previous welding process has a great impact on the quality of teaching and playback welding, and repetitive teaching is time-consuming and laborious. The new Nvision 3D vision weld seam guidance system eliminates repetitive teaching and significantly improves production efficiency.
Ⅴ.System Applications
The 3D vision weld seam guidance system can improve production efficiency and reduce the defective product rate. It is usually applied in occasions where repetitive workpieces are involved and certain welding precision is required, such as:
- Welding of the pole column of the battery top cover.
- Welding of the module Busbar.
- Welding of the top cover of the square shell battery.
- Welding of the explosion-proof valve of the top cover.
- Welding of the hairpin motor.
Practical application examples
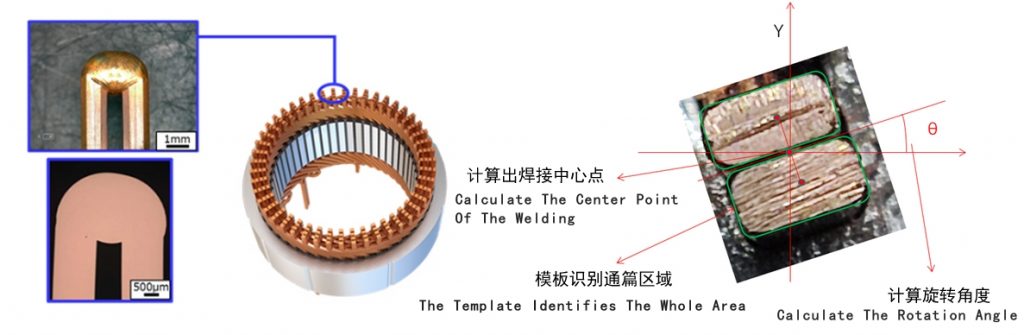
- Based on the matching template, find the coordinates of the welding center point and calculate the X and Y offsets of the workpiece.
- Based on the template coordinates, fit a straight line parallel to the weld seam to calculate the offset angle of the copper sheet, calculate the angle compensation value to adjust the mechanical module to weld the copper sheet in the correct posture.
Conclusion
The Newlaz 3D Vision Weld Seam Guidance System will continue to improve and is expected to contribute to the development of the welding industry in the industrial manufacturing field and promote the optimization and improvement of welding processes.