Introduction
Benefiting from the booming development of new energy vehicles, the three-electrical system (motor, battery, and control system) has achieved significant technological breakthroughs. In the field of motors, the Hair-pin Motor has replaced the traditional round wire motor as the mainstream trend. Its advantages mainly lie in high power density, wide speed range, large starting torque, and wide-ranging high-efficiency zone. However, unlike the relatively simple and mature production process of traditional round wire motors, the stator winding form of the Hair-pin Motor is still developing continuously. From the initial I-pin form to the current mainstream U-pin, and even future trends such as X-pin, W-pin, and Umini, all of these issues are related to the welding problem of pin terminals. As a supplier dedicated to researching laser welding solutions for drive motors,NewLaz has proposed targeted solution.
Hair-pin motor laser welding solution
The X-pin winding, U-pin, and Umini winding are the closest in manufacturing process similarity, with significant differences mainly in the twisting process. X-pin has no straight segment, making twisting difficult, and the flat wire terminals formed after twisting have an uneven surface without a flattening process, without a cut-flat process. Additionally, it is necessary to ensure the climbing distance between electric fields.
In existing technology, laser welding technology has been proven to be a key process for producing the stator of Hair-pin Motor. For laser welding equipment for X-pin terminals, as the exposed copper wire of I-pin, U-pin, or Umini terminals is longer, has a flattening process, and there is no height difference between the joints, the workpiece can be easily designed to ensure consistent joint assembly conditions, making it easier to perform normal welding operations on these three types of terminals.
However,for X-pin,challenges and difficulties in welding technical still exist, including:
- The end face of the X-pin joint is uneven, and there are changes in the wrong side of the height;
- In view of the gap, horizontal dislocation and other easy to exist light leakage, edge and corner of the phenomenon of non-melting;
- The X-pin connector copper flat wire terminal assembly has poor consistency, and the accuracy and precision requirements of the visual guidance system are very high.
NewLaz has developed a pre-welding recognition system and post-welding quality inspection system for Hair-pin motor welding, which combines 2D/3D camera and is compatible with I-pin, U-pin, Umini and X-pin connectors. The 2D visual system has a large photo range: it adopts coaxial vision to obtain the coordinates of the Pin welding points and assigns different process numbers to each Pin, completing pre-welding visual guidance.The 2D visual system has a large photo range: using coaxial vision, the coordinates of the solder joint points are obtained, and different process numbers are assigned to each pin, completing pre-soldering visual guidance.
- Product type:completely divided into 8 ROI areas, 8 photos, 4 * 6 points each time, a total of 192 solder joints;
- Pre-welding positioning inspection:NewVision-2D/3D visual inspection subsystem;
- Welding Head:NewScan-2D/3D Galvanometer On-the-fly Laser Welding Head;
- Laser:RFL-ABP circular spot laser;
- Post-welding quality inspection:NewQISys Quality Inspection System;
- Total beat: photo + welding beat <35s.
3D visual system is applied to detect X-pin connector assembly clearance, horizontal misalignment, deflection angle, and vertical misalignment, etc.
I-pin/U-pin/Umini motor laser welding solution
The 2D vision system uses the coaxial camera to obtain the coordinates of the Pin solder joint, and controls the offset of the vision algorithm to complete the identification and guidance before welding.
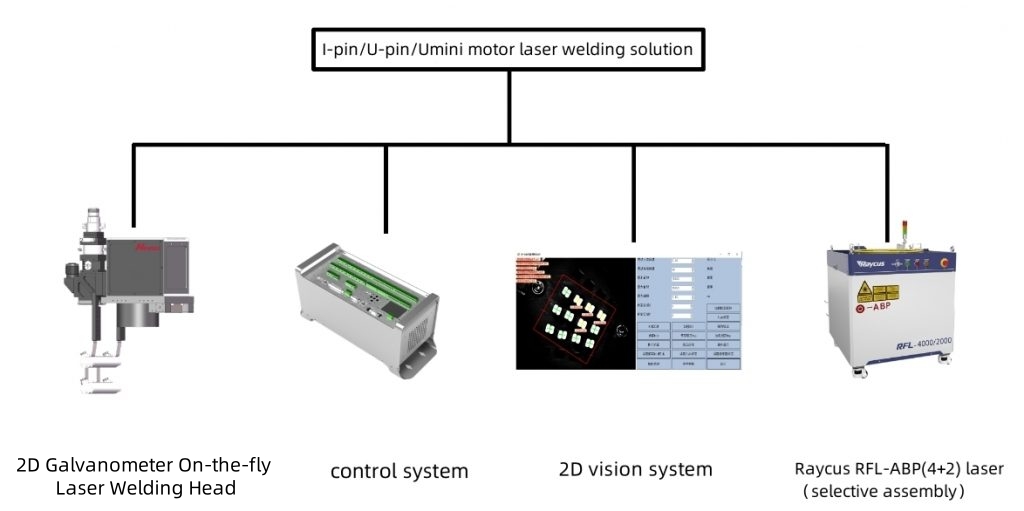
X-pinmotor laser welding solution
The exposed copper wires of the X-pin motor’s terminal connectors are relatively short, the welding points are below the workholding fixture, and there is a height difference after rotating the head. Therefore, it is necessary to use a combination of 2D camera photography recognition and 3D vision detection to guide the welding process based on the height difference of the workpiece.

Process expert database
NewPWED, a laser welding process expert database dedicated to X-pin laser welding, has built-in multiple PIN welding process parameter groups, which matches different assembly states of the joints to be welded, and choose the corresponding welding process parameter group for welding according to the demand, realizing intelligent, high-efficiency and high-quality welding.
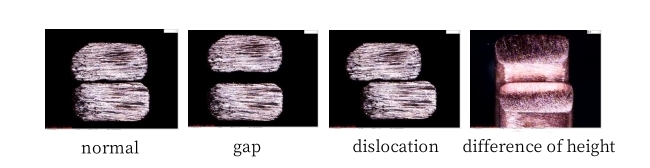
Advantages of System:
- High efficiency production: stator welding completion time of 6 layers of winding is <27S / P, welding completion time of 8 layers of winding is <35S / P;
- High quality welding: high precision high speed vibrator welding head + high quality visual recognition + high adaptability welding process;
- Process expert database: it can intelligently match joint status and welding process, and provide joint welding quality and qualified rate;
- Integrated control: independent design and development of embedded system to realize direct communication between visual system and mirror system, with high matching;
- Housekeeping service: 7 * 24 hours of service response, experienced service engineers, fast maintenance speed (core components are independent), customized function development.
The comprehensive solution for the NewLaz Hair-pin Motor Welding Subsystem effectively detects, identifies, and analyzes the assembly state of the joint, while simultaneously providing real-time monitoring of the welding state of the pin line terminal. Furthermore, it intelligently manages the output parameters, ensuring precision and efficiency throughout the welding process.At the same time, the laser welding process expert database is developed to match the various assembly states of the welding head to be welded, and the corresponding welding process is called out according to the requirements, so as to realize the intelligent high-quality and efficient welding production of the flat wire motor.