前言
随着新能源汽车对动力电池性能要求的提高,激光焊接作为一种高效精密的焊接方式,在新能源汽车制造过程中,广泛应用于白车身和动力电池的焊接,以满足新能源汽车制造轻量化和安全性能提高的需求。新耐视飞行焊接高度实时跟踪视觉系统通过3D相机识别动力电池中心高度,实时跟踪飞行焊接效果,提高了生产节拍;高度测量和飞行焊接合并到同个工位完成,精简了生产流程,使飞行焊接过程更加自动化和智能化。
一、传统检测方式的弊端
- 寻位方法引起的焊接延迟
传统的寻位方法需要通过3D相机将全部待焊部位采集完毕后,分析得出焊接部位的位置高度信息,焊接过程明显滞后于3D相机采集数据过程。
- 双工位焊接流程繁琐
传统的焊接流程都分为两个工位,定位工位和焊接工位交替进行,不仅占用空间,而且机器人需要在定位工位预先单独测量动力电池高度信息,设定完轨迹高度后,再进入焊接工位开始焊接,流程繁琐。
二、系统简介
1.系统原理
通过在振镜焊接头前置一个3D相机实时采集动力电池表面高度,分析待测表面高度偏差值并及时调整振镜高度,实现实时高度跟踪飞行焊接的效果。
2. 系统构成
飞行焊接高度实时跟踪视觉系统主要包含3D相机、工控机(含视觉软件),同时搭配飞行焊接系统、机器人(或三轴平台)、PLC等。
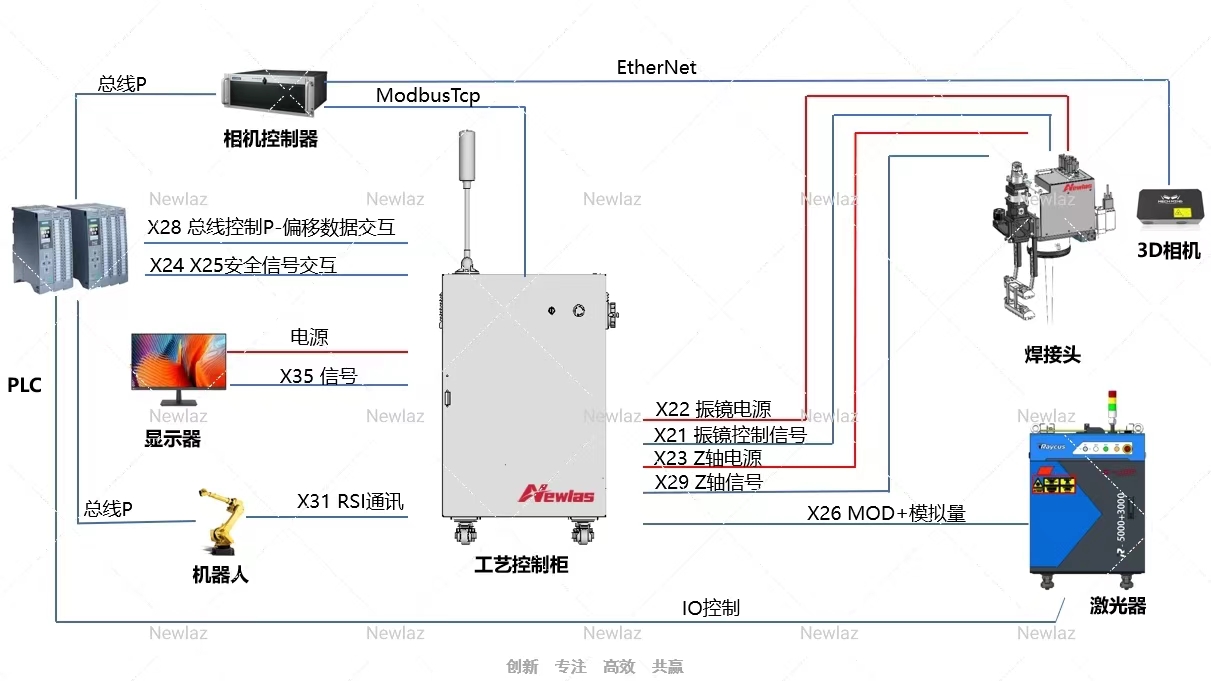
新耐视飞行焊接高度实时跟踪视觉系统构成
三、系统优势
- 高度测量与焊接过程时间重合,有效提高生产节拍;
- 高度测量和飞行焊接在同个工位完成,能有效节约生产成本,提高场地利用率;
- 点云分析与数据发送过程稳定,总体耗时小于0.2s,保证跟踪过程的可靠性;
- 可灵活应用于机器人平台和三轴平台,高度测量精度<0.1mm;
- 可最高适配飞行速度 300mm/s;
- 具备巴片高度、高度极差、位置、间距等防呆判断。
四、系统应用
主要适用于新能源动力电池BusBar激光飞行焊接过程的巴片高度实时测量与反馈,可及时调整振镜飞行焦点高度,保证焊接质量。
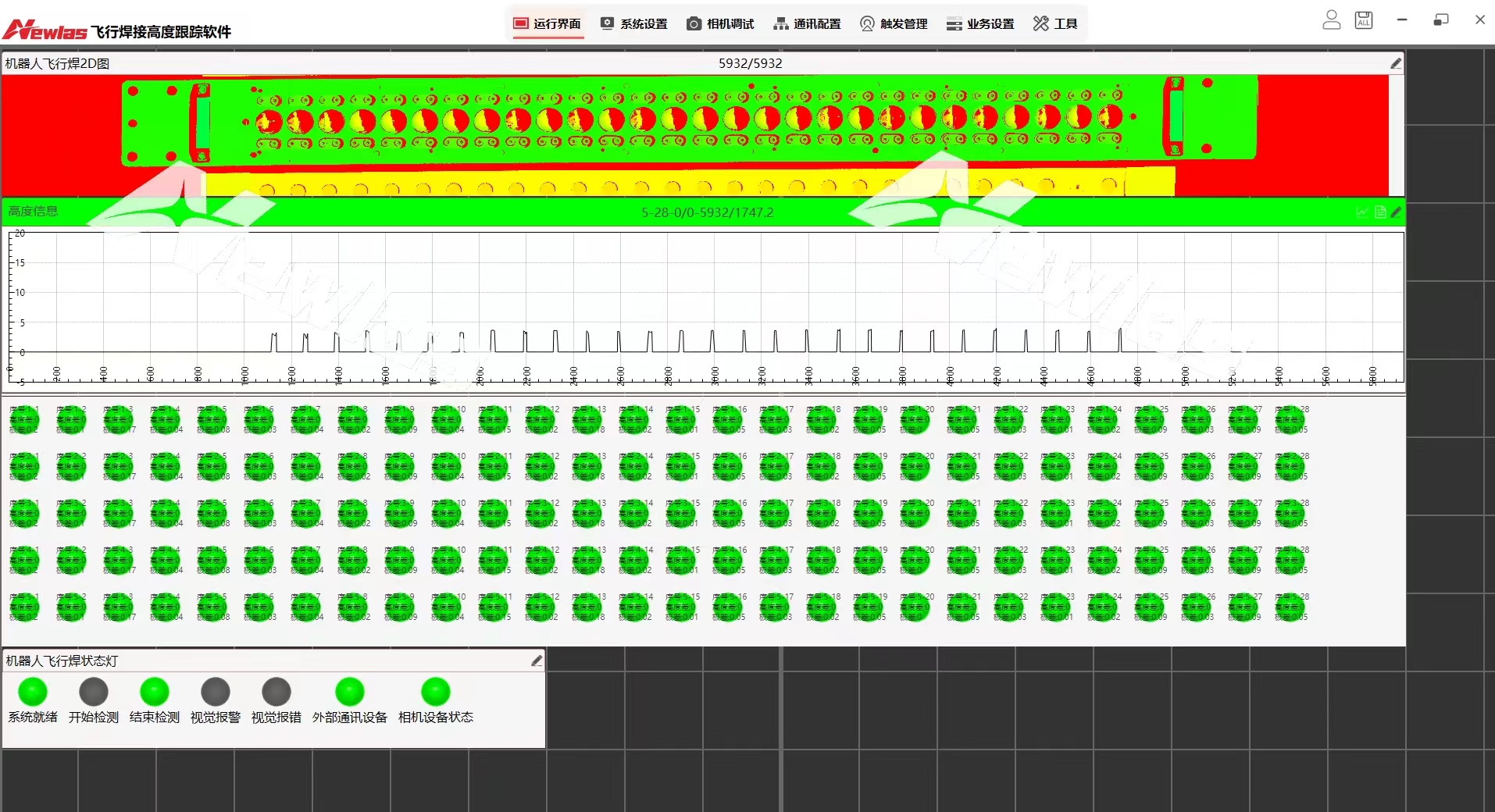
视觉跟踪测量软件——NewVision-T3
结语
随着科技的不断进步和制造业的持续发展,新耐视将围绕激光焊接高质高效降本的需求,不断升级飞行焊接产品的性能包括相关的检测系统,以适应更复杂和多样化的生产场景,进一步提高焊接质量和效率,实现更高程度的自动化和智能化,为制造业的转型升级提供有力支撑。