由于铝合金固有的物理性质,比如对激光低的吸收率、合金元素的低沸点、高的热导率、高的热膨胀系数、相对较宽的凝固温度区间、高的凝固收缩率、低粘度以及液态下高的吸氢性等,因此在激光焊接过程中容易产生气孔、热裂纹等缺陷。
其中,气孔是铝合金激光焊接过程中最容易产生的缺陷形式,它会破坏焊缝金属的致密性,削弱焊缝的有效截面积,降低焊缝的力学性能和耐腐蚀性,因此必须采取有效措施防止气孔产生,提升焊缝内部质量。
通过焊前表面处理方式抑制焊接气孔
焊前表面处理是控制铝合金激光焊缝冶金气孔的有效方法,通常表面处理方法有物理机械清理、化学清理。
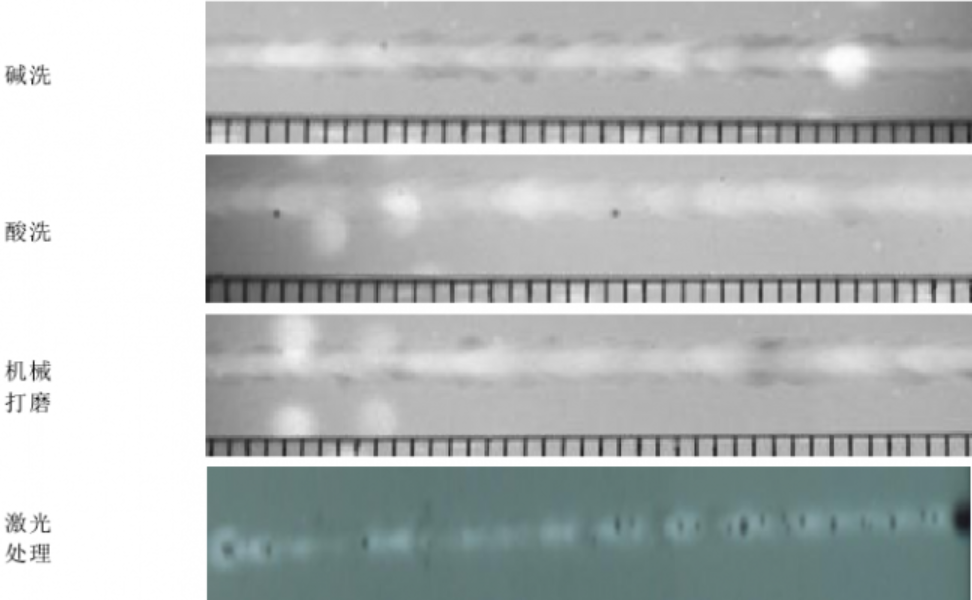
经过对比,采用化学方法处理试板表面(金属清洗剂清洗-水洗-碱洗-水洗-酸洗-水洗-干燥)的流程处理最好。其中碱洗用25%NaOH(氢氧化钠)水溶液去除材料表面厚度,酸洗用 20% HNO3(硝酸)+2% HF(氟化氢)水溶液中和残留的碱液。试板表面处理后在24小时内实施焊接,试板处理后停留时间较长时焊前装配再用无水酒精擦拭。
通过焊接工艺参数抑制焊接气孔
焊缝气孔的形成除了与焊件表面处理质量有关,还与焊接工艺参数相关。焊接参数对焊缝气孔的影响主要体现在焊缝熔透情况,即焊缝背宽比对气孔的影响。
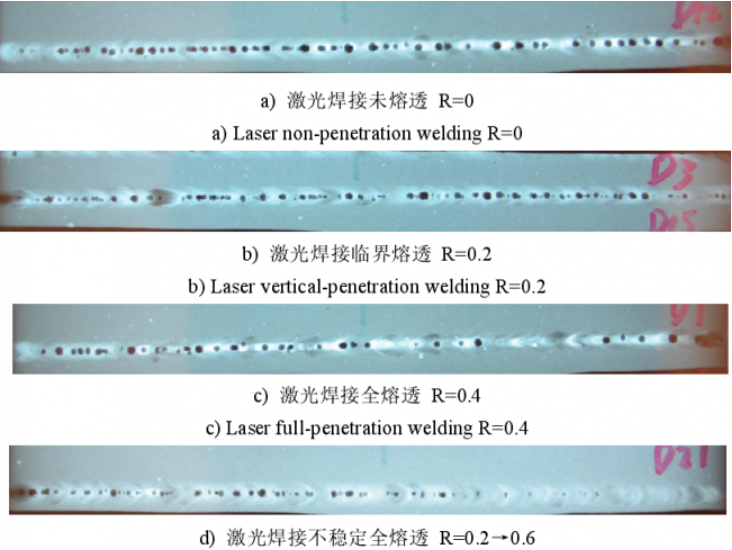
通过测试可知,焊缝背宽比R>0.6时可以有效改善焊缝中链状气孔的集中分布,当背宽比R>0.8 时,可以有效改善焊缝中大气孔的存在,并很大程度上消除了焊缝中气孔的残留。
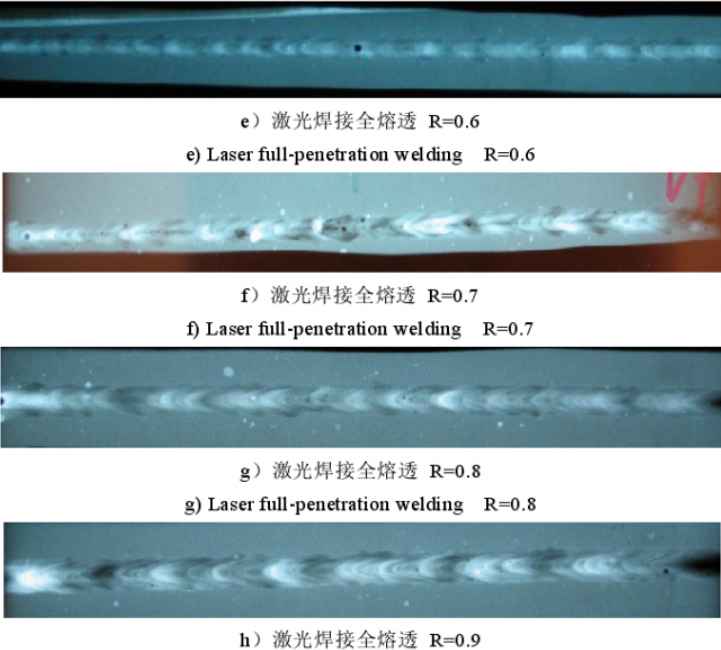
通过正确选择保护气体及流量抑制焊接气孔
保护气体的选用直接影响到焊接的质量、效率及成本,激光焊接过程中,正确的吹入保护气体可以有效减少焊缝气孔。
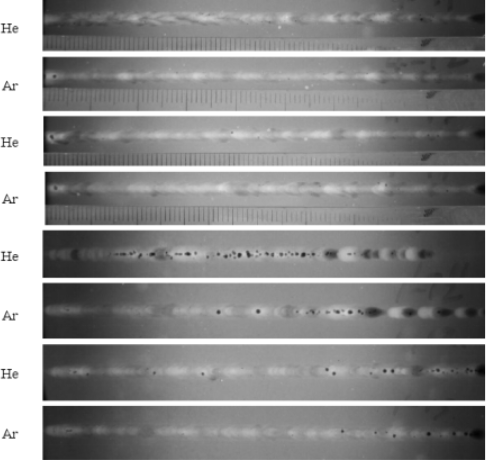
采用Ar(氩气)和He(氦气)对焊缝表面进行保护,在铝合金激光焊接过程中,Ar和He对激光的电离程度不同,造成焊缝成形不尽相同。结果可见,选用Ar作为保护气体所得焊缝的气孔率整体少于选用He作为保护气体时焊缝的气孔率。
同时我们也要注意,气流量过小(<10L/min)焊接产生的大量等离子体无法吹走,使得焊接熔池不稳定,气孔形成几率增加。气体流量适中(15L/min左右)等离子体得到有效控制,保护气对溶池起到了很好的防氧化作用,气孔最少。过大的气流量伴随过大的气体压力,使得部分保护气混入溶池内部,使气孔率上升。
文章来源:OFweek激光网